4 min read
Preparations for Next Moonwalk Simulations Underway (and Underwater)
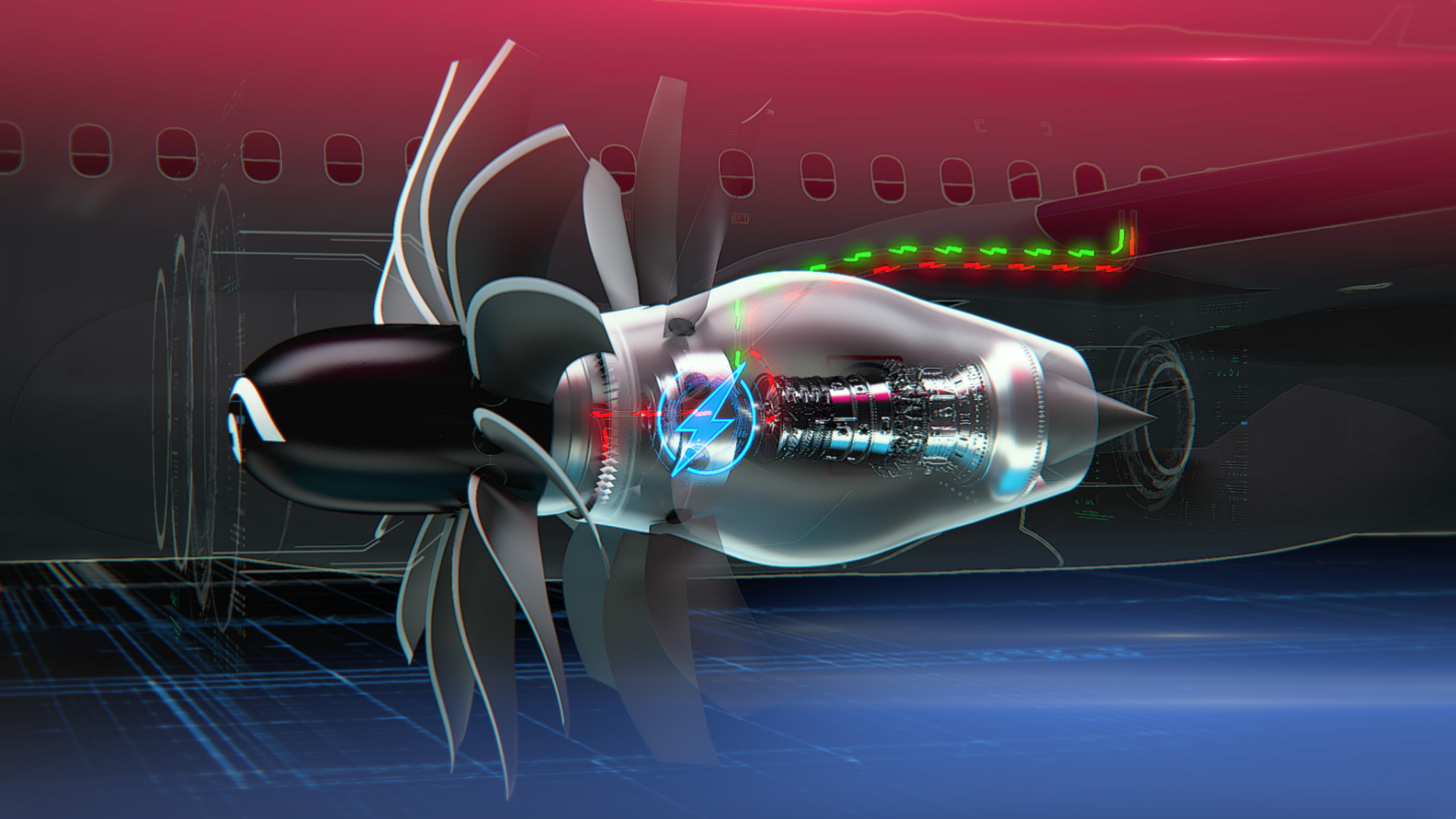
NASA, alongside industry, will soon begin designing a new jet engine concept for the next generation of ultra-efficient airliners — officially graduating to the project’s next phase.
As part of NASA’s goal to make the aviation industry more sustainable, the agency is developing a small core for a hybrid-electric turbofan jet engine that could reduce fuel burn by 10% compared to today’s engines.
A jet engine’s core is where compressed air is combined with fuel and ignited to generate power. By making this core smaller, fuel efficiency can be improved and carbon emissions reduced.
The goal of the project, named Hybrid Thermally Efficient Core (HyTEC), is to demonstrate this compact core and have the technology ready for adoption in engines powering next-generation aircraft in the 2030s. HyTEC is a key component of NASA’s Sustainable Flight National Partnership.
To achieve its ambitious goal, HyTEC is structured in two phases:
- Phase 1, which is wrapping up, focused on selecting the component technologies to use in the core demonstrator.
- Phase 2, starting now, will see researchers design, build, and test a compact core in collaboration with GE Aerospace.
“Phase 1 of HyTEC is winding down and we are ramping up Phase 2,” said Anthony Nerone, who leads HyTEC at NASA’s Glenn Research Center in Cleveland. “This phase will culminate in a core demonstration test that proves the technology so it can transition to industry.”
The End of the Beginning
Before researchers could start the design and build process for the core, they had to explore innovative new materials to use in the engine. After three years of notably fast progress, HyTEC researchers came up with solutions.
“We’ve been laser-focused since day one. We began the project with certain technical goals and metrics for success and, so far, we haven’t had to change course from any of them,” Nerone said.
To shrink the size of a core while maintaining the same level of thrust, heat and pressure must increase compared to standard jet engines used today. This means the engine core must be made of more durable materials that can withstand higher temperatures.
In addition to conducting materials research, the project also explored advanced aerodynamics and other key technical elements.
What Comes Next
Phase 2 builds on Phase 1 to create a compact core for ground testing that proves HyTEC’s capabilities.
“Phase 2 is very complex. It’s not just a core demonstration,” Nerone said. “What we’re creating has never been done before, and it involves many different technologies coming together to form a new type of engine.”
Technologies tested in the HyTEC program will help enable a much higher bypass ratio, hybridization, and compatibility with sustainable aviation fuels.
The bypass ratio describes the relationship between the amount of air flowing through the engine core compared to the amount of air bypassing the core to flow around it.
By decreasing the core size while increasing the size of the turbofan it powers – while maintaining the same thrust output — the HyTEC concept would use less fuel and reduce carbon emissions.
“HyTEC is an integral part of our RISE program,” said Kathleen Mondino, who helps lead RISE program technologies at GE Aerospace. “GE Aerospace and NASA have a long history of collaboration to advance the latest aviation technologies. The HyTEC program builds on this relationship to help chart the future of more sustainable flight.”
Another piece of the puzzle is hybridization. HyTEC’s hybrid-electric capability means the core will also be augmented by electrical power to further reduce fuel use and carbon emissions.
“This engine will be the first mild hybrid-electric engine, and hopefully, the first production engine for airliners that is hybrid-electric,” Nerone said.
About the Author
John Gould
John Gould is a member of NASA Aeronautics' Strategic Communications team at NASA Headquarters in Washington, DC. He is dedicated to public service and NASA’s leading role in scientific exploration. Prior to working for NASA Aeronautics, he was a spaceflight historian and writer, having a lifelong passion for space and aviation.